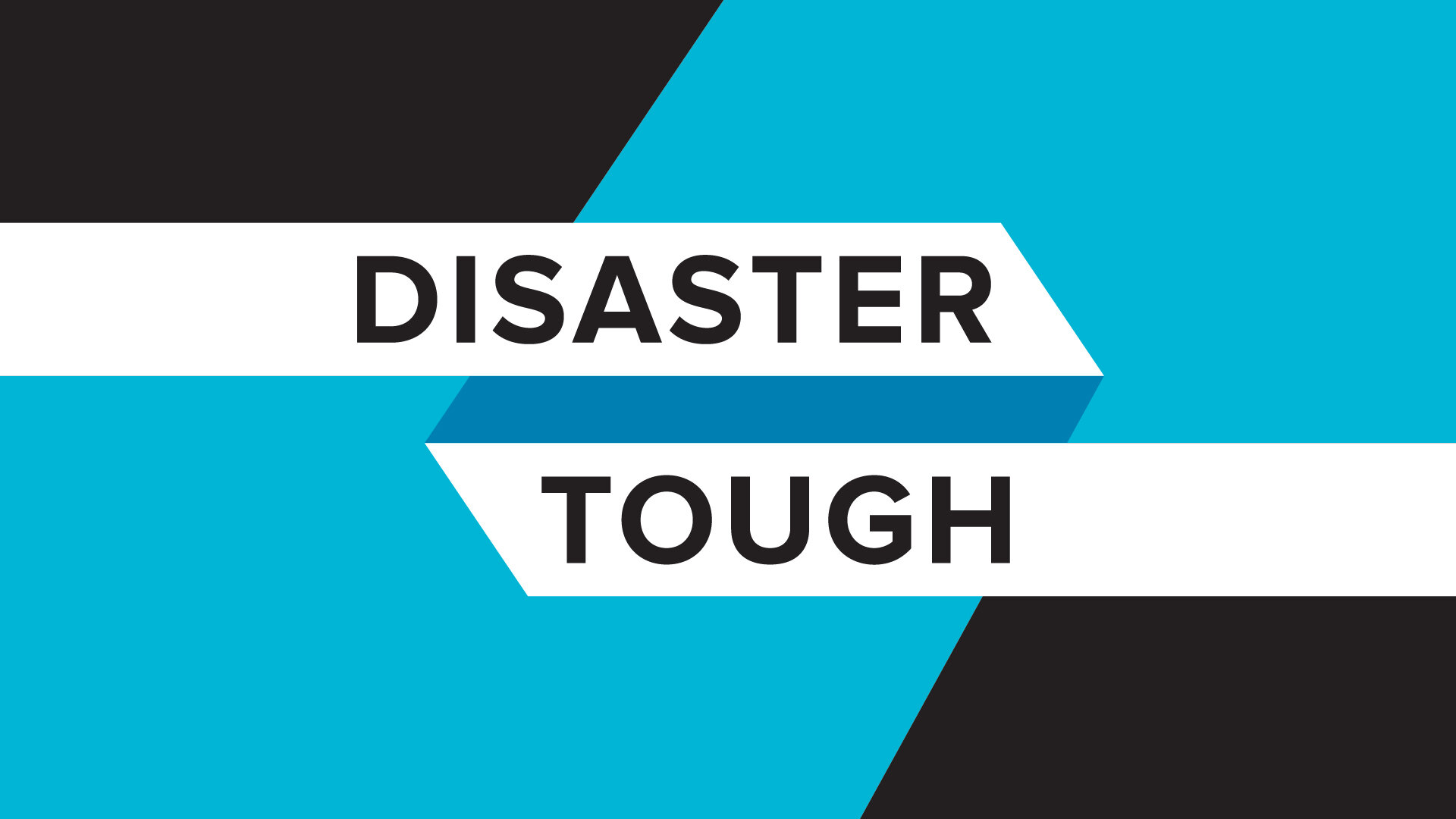
#82 Amazon's IT Risk Management & Supply Chain Considerations: Interview with Andrew Owlett
Andrew Owlett is the Senior Manager, Global Business Continuity and Risk Intelligence working in OpsTech IT, WW Operations for Amazon. He talks to us about business impact from the IT perspective.
Conducting a business impact analysis, understanding the Global Supply-chain, and working in concert with technologies is an absolute necessity for the emergency manager of tomorrow. Amazon is a behemoth in the supply chain world and Andrew helps run their IT systems from the perspective of business continuity. He shares his thoughts on supply chain, data science, and how the pandemic has impacted business.
This Podcast has moved to the Readiness Lab.
Host: John Scardena (0s):
You've just entered the Disaster Tough Podcast, the place for emergency managers, first responders and humanitarians who want to get the job done. Stories, lessons and tips are provided by field experts. This show is owned and operated by professional emergency managers at Doberman Emergency Management. We apply disaster tough logic by protecting life, property, and business continuity through planning, mitigation, and training. Check us out at dobermanemg.com or click on the show notes.
Radio comms just got a major breakthrough with the L3 Harris XL extreme 400P, is the newest and toughest radio out there built by their space and tactical teams. The XL extreme series can take a beating 1700 degree blast of heat, repeated three meter drops, rain, salt water, you name it, the XL extreme series by L3Harris can take it. Visit L3harris.com to schedule your demo today.
The battle to monitor and contain COVID-19 just got exponentially better for us. We are officially introducing an electronic reusable yes, reusable COVID-19 test through our sponsors. It's called the COVID plus test created by Tiger Tech distributed by FS Global. This is the first FDA authorized rapid non-invasive pre screener. It's extremely easy to use. Forget those one-time use swabs, this is a disaster tough technology. For more information on the COVID plus test check out our show notes.
Host: John Scardena (1m 38s):
Welcome back to the show, everybody. It's your host, John Scardena. I am very excited for this episode. We've been talking to Andrew for some time trying to get them on the show because we're really excited about the type of perspective he can bring to emergency management and business continuity. So Andrew comes from the Amazon world. Yes, Amazon the Amazon, and he can talk about all that perspective there. Andrew, welcome to the show.
Guest: Andrew Owlett (2m 7s):
Hey John, thanks so much for having me today. I'm super hyped to be here.
Host: John Scardena (2m 11s):
Yeah, absolutely. So we were just kind of joking around before the show. You have quite the title and roles and responsibilities there to job. Can you tell our audience what your title is at Amazon?
Guest: Andrew Owlett (2m 23s):
Yeah, so I'm senior manager of global business continuity and risk intelligence specifically within Amazon robotics. Even more specifically within the, really the Amazon worldwide operations information technology node. So we're the people that deploy source and then we recycle, I guess the technology that goes into fulfillment centers worldwide.
Host: John Scardena (2m 53s):
Okay. So a little known fact about me is I worked for another tech company. There are fruit and I was the head of business intelligence there for a while. I was doing project management stuff there for the internal, some of our 300,000 employees or whatever. So I can definitely understand the perspective of for-profit entities wanting to do business continuity and wanting to make sure that, you know, what we call them, tears, right. When something had happened, if it impacted the immediate business or long-term moments, who try to, we'd have to manage it that way. I got to see this perspective of emergency management from the perspective of systems breaking, not just critical infrastructure, but for organizational perspective. I think you can provide a lot of insight there. Just to start it off, the impact of business and global operations and in Amazon and your role there specifically, to robotics and making those systems work, what type of impact does that have on day to day? Are issues happening every day or are you looking at more of the long-term preventative or is there a lot of mitigation? What are the different components of the disaster life cycle? Are you hyper-focused on in your job?
Guest: Andrew Owlett (4m 19s):
Yeah, so my team and I focus a lot on super proactive sensing and intelligence. First, we believe that if you have really good intelligence on what's going on in the world, and you can map that to how that intelligence could impact your assets, whether you're at Amazon, like I am, or other companies, it allows you to be more proactive versus reactive when something happens. So we put a lot of effort into hunting for what are those threats vulnerabilities and have there's that change every day and then map that back to our business to see what the impact would be from.
Host: John Scardena (5m 5s):
Okay so let's break that down a little bit, because what you're talking about as a hazard vulnerability assessment, but unlike, I would say, what a government would do. So I'm trying to compare government to organizations. So government, we have our hazard mitigation plan, which says a firearm and it has a vulnerability assessment every five years. Well, you're talking about as a constant need to have situational awareness of both external and internal vulnerabilities. How do you get to the preventative side of that. So when you're talking about the intelligence gathering, what are some resources that you could provide to the field that say, hey, for an organizational emergency managers listening to this, right? It's their job to do what you do on a different scale or a different company, or some resources that they would have to pull in to have that situational awareness.
Guest: Andrew Owlett (5m 54s):
Yeah. So, I mean, going back to what you said, I mean, doing some sort, a THIRA or hazard vulnerability assessment HVA and the public sector, that’s the problem that I felt. So I came from public sector into private and the problem is that the threat landscape literally changes every day. If you only do an assessment once a year or once every couple of years, you're really not accurately painting a picture of what is your true risk to business impact, so we take the approach of constantly assessing. So we ingest data, we assess data through open source intelligence first and also closed source intelligence, which is a little bit different. We do that through a variety of different mechanisms, having analysts support, tech support, and then we provide actionable insights for our stakeholders to take based on what we're seeing external to Amazon. So if I was an emergency manager in a locality and I didn't have access to, you know, kind of funding and resources, the first place I would go to is something as simple as like a search engine, like Google and maybe build in an alert for X, Y, and Z of this sort of happen. I need to be notified about that it's cheap to zero costs. It takes a little bit of time and super helpful.
Host: John Scardena (7m 22s):
Yeah I think that's a good idea, a good idea to build on those alerts, whether it's a news alerts or otherwise, I take it, you know, if we're talking about building that foundation of situational awareness, being on the national team was the national strike team was purely for response. We had constant situational awareness between our settle and between my myself, who I did GIS geospatial intelligence for the team. So every day constantly, we were not just getting the notifications, but we are doing threat assessments based off of a US perspective of what could impact and where could impact the critical infrastructure of the populations of social vulnerability, all that stuff. When we inverse more in response, well, you're talking about is like a, I wouldn't say like a pseudo response, but you're constantly getting that intelligence. I'm sure you're doing fairly frequent briefings based off of that intelligence that comes through, I'm thinking of it almost like your ops periods, like a 24 hour ops period every morning. You're probably sending a brief out if I'm going to guess.
Guest: Andrew Owlett (8m 32s):
Yeah. So our cadences are a little bit different, but because specifically, even more specifically to just emergency management and business continuity, like at a high level, narrowing that down, we're focusing very much in the supply chain space. So we want to be on the cutting edge of supply chain intelligence that's outside of Amazon, but also there's a lot of sources that we get into Amazon directly from our suppliers that we need to assess as well. So meshing those two things and in some cases, three things together, because there could be another category there as well takes a lot of analytical insights, a lot of just understanding of the business. You have to understand the business you're in, you have to understand where those dependencies are and how they can. So, yeah, so going back to what you said, the frequency can be 24 hours, it can be every two weeks, it can be every week, depending on like the type of environment you're in, it's consistently customer.
Host: John Scardena (9m 42s):
So let's break that down because you're talking about supply chain and supply chain is very popular right now. I'm going to look at it first from the perspective of, as Amazon is both a supplier and works with millions of suppliers. You know, you have a unique circumstance where your supply chain is both could be interrupted by internal processes. But also if people let's say, I don't think we're even close to there yet. I mean, it probably won't be for ever, but Amazon prime is like the favorite function of everybody, right? You get Amazon prime and get things within two days. Now you have a population that is used to having that function and supply chain is interrupted even more for a major product within Amazon. Then you start to have a different side of the business impact of customer service issues, let alone, you know, your business SOP is now impacted. How does Amazon decipher working with you? Because you've said it a few times outside of Amazon now a few times, how do you decipher, okay, high priority product? Is it based off of revenue, like your business impact analysis? Is it impact on revenue? Is it impacted on time? Is it impacted on, you know, another factor that you know, that you have to consider that maybe the general population doesn't have to consider?
Guest: Andrew Owlett (11m 11s):
Yeah. So, I mean, with, with any, with any type of program in the space, I mean, if you have to, you have to know who your customers are and you have to understand what's important to them. And that's how we kind of build our programs. So we, we have internal facing customers that they, they want products and services at a certain time and a no-fail environment. And we have to prioritize those first based on what our customers feel are the most important to them. And there's, there's a lot of things that are important to our internal customers. And a lot of things can beat with each other, but as a business, if, if things are going to impact our customer, that's number one, that's, that's always number one, we're obsessed over them, whether they're internal or external.
Guest: Andrew Owlett (11m 59s):
So, I mean, we prioritize our efforts based on customer demand and priority and then also from a business impact analysis perspective, just anywhere, I mean, money, money is super important, right? If a particular function is going to cost the business a lot of money, that's a higher priority than something that maybe isn't as critical. It doesn't have as much financial offs, if any. So you were talking about business impact analysis. I mean, that's super critical. I mean, from a supply chain risk perspective, which is a lot of the world that I live in it's a basis for figuring out where your dependencies are, people, processes, technology. How do you rely on all of that? Whether it's third party, whether it's internal party, it's super important to have that kind of laid out first.
Host: John Scardena (12m 52s):
So let's talk about the elephant in the room, supply chain, it's all in the news right now. There's, you know, politicians will say things like, you're not going to get your Christmas presents or stuff like that. But every time I use Amazon, I'm still getting the things that I want from the Amazon prime is still available. So from Amazon's perspective of supply chain right now, obviously you have the forward facing message of everything's okay. But that's not the audience we're talking to. We're talking to an audience of emergency managers who get that not everything's okay. But still a lot of things probably still are. Okay. So from your perspective of talking to emergency managers in the field about supply chain, who understand supply chain from a disaster response perspective, especially a large-scale disasters, what is your view of like what's happening in the world of supply chain right now? Is that as dire as it's made out to the news, is there certain functions that they're not really focusing on, that they should focus on? How do you build redundancy? I mean, I have so many questions on this topic. I will let you determine why you want to talk about it there, but what do you think about supply chain right now in the world?
Guest: Andrew Owlett (14m 3s):
Yeah, I mean, one of the things that we're seeing across the world right now, is that because of consumer electronics spending really skyrocketing during the beginnings of COVID, whether it's people working from home or taking classes from home, because they're in school or whether medical technology is needing, it increase their output to be able to fight like COVID. There was a lot of demands placed across a whole bunch of industries at one at one time, especially in the technology space. A lot of what we're seeing now are the repercussions of what started two years ago, almost two years ago. Then also seeing the ripple effect across other industries, because when COVID first started, you know, people may not be communicating to work all the time. Maybe auto use is going down, but now people are starting to commute into work again and auto use is going up. We also see in the geopolitical landscape, more and more of an emphasis on sustainability across the board, more an emphasis on electric automobiles and with all of that causes, you know, some other ripple effects there as well, because you have all of these different industries trying to ramp up right now, and they're all competing against each other. There's only so much at the ground floor level, quote, unquote, ground floor level.
There's only so much raw material that can be produced as it gets at a given time. So they're either constraints at the very bottom levels of the supply chain, like raw material or there's constraints with how are we going to transport all this product quickly to meet customer demand. There's only so much shipping container capacity in the world right now. That's a big, hot topic, certain on CNN, Fox news, CNBC, etc. You'll see that out there and if you can't go be a shipping container, what are your other mechanisms to get product from point a to point B while you still have air. In some cases you have rail, but costs for that and then speed are all completely different. So you start seeing your ripple effects across, you know, a whole bunch of industries because of what happened two years ago. Those ripple effects, you know, they keep going out and out and out, and then consumer demands changes all the time and what we want changes all of the time. The one thing that remains constant though, is that when we want something, we want it now and we want it quicker and faster than ever before. So I mean, in the future and in the next six months to a year, I mean, those, those demands will completely continually escalate and, you know, people want their stuff, they want it faster and that's not going to change. That's the one thing that won't change over the next year. So as supply chain professionals. So, you know, there's definitely a lot of pressure on the shoulders to figure out how to handle situations.
Host: John Scardena (17m 8s):
Yeah, definitely like, is that all next year, I predict the next 18 months, two years, three years, even trying to kind of work this out and trying to level out, maybe even beyond. So for the audience sake, I'll give you a real world example of how this, what you're talking about applies to them, especially if they're doing natural disasters and why that matters and then I'll talk about some of the work I just did in LA here, Puerto Rico, 2017, hurricane Maria, the strike team that was sent there, unfortunately didn't understand. This is why this is so important to understand the impact of supply chain and supply chain and how it moves the system, it moves, you're talking about air, land and sea, and it's an island. So they didn't understand both the regulations, the laws that had to be utilized there. Also the requests I had to be like, there was like a five day minimum request is 2017 is not pandemic life. There's a five day delay there and they didn't understand how early they need to start ordering resources in order to catch up. Now we don't have any resources for several days and the famous example is that the planning section, she was taking pictures on the beach because they had nothing else to do. Lo and behold, the entirstrike team was fired and they should have been, I'm super critical of that.
I was in hurricane Harvey at the time when I was blown away by the lack of speed and understanding of supply chain, because supply chain is response. Supply chain of use our team supply chain of infrastructure, supply chain of all these things that have to be put in place. So just even materials like food, basic food and water, and they didn't understand it. So if you're an emergency manager and you're in the Midwest or you're on the west coast and you have to deal with a major earthquake and all of a sudden, you know, your port's taken out or you're in Puerto Rico and you're on an island like these implications matter. So that's the real-world example. Then about a month ago, I was in a port of Los Angeles and I saw I was actually on a boat with the Coast Guard. I saw the million, you know, shipping containers out there and like, hey, and they were talking about the length of time added, before it was like 12 to 18 days. Now they're looking at 25 to 40 days on the water and to constraints it's having. As a supply chain company, I'm an Amazon is truly a supply chain company in terms of its major perspective and having to work with that. I mean, you have security risks, you have consumer increases, you have so many different constraints. Now you're talking about raw material and even getting that raw material to a place where it can even be fractured and so your delay could happen even before the process really even begins before you even have a product to deliver. This is really fascinating to think about for sure.
Guest: Andrew Owlett (20m 13s):
Yeah and I think going back to your example of yeah, Puerto Rico is an island and you know, that just adds so many degrees of complexity there as well, because there's a lot of things in the continental United States. Then in other parts of the world that we take for granted, and one of the biggest things is how we're, connected to major sources of infrastructure and, and so much more. I island so many unique considerations and there’s definitely a lot of different planning facets that need to go into that. But one of the things that I would suggest to anybody out there that hasn't necessarily placed a lot of emphasis into what is their supply chain look like? You know, going back to something you mentioned earlier, business impact analysis is super important to understand what you do and how you do it. Then who's involved and what's involved in that, who's involved, what's involved piece. It can mean that, you know, you're working with internal stakeholders or external stakeholders as well. How much do you rely on these stakeholders to X, Y, and Z? What do you rely on them for dig a little bit deeper there? Then, you know, that’s the most basic level of analysis and more moderately advanced level of analysis is looking like where do my supplies come from geographically? Because that's super important and how do they come to me geographically? What mode of transportation? Who's bringing the supplies to me? Do I have a backup supplier in case something happens, the primary supplier, you know, little things like that really go a long way. Then you can even take those level of analysis, even deeper to see, how does your supply chain really map together?
Host: John Scardena (22m 8s):
Yeah, you're talking a lot about memorandums of understanding too, right? I mean, that just doesn't happen. Amazon kind of has the weight there where they can call and say, hey, you're now the primary for the next six weeks. But in most cases, you're going to have to have MOU in place to say, hey, if a system is broken on one end, we need to have this already. The understanding of what the supply is, whether it's power or otherwise needs to already be put in place. So you're hitting on a lot of keys there. I'm going to geek out really hard here for a second thinking of my business intelligence and or business impact analysis hat. Do you deal a lot with Q theory and nor do you know what Q theory is?
Guest: Andrew Owlett (22m 52s):
I don't.
Host: John Scardena (22m 54s):
Yeah. So basically the example is a bank teller. If a bank teller takes 10 minutes to process a person and we have one person come in exactly every 10 minutes, you'll have no queue. You'll have no nobody waiting, but that's not reality. So we do in terms of a data science we'll use like AAR or we'll use some other scripting capabilities for data, data science. And we'll say, okay, if one, the math works out that a fee of one bank teller that takes 10 minutes on average, and you have people coming in like normal. By the end of the day, your queue will be five hours and 48 minutes in an eight hour day, just because of the backup that keeps happening. If you add one other bank teller, that bank teller also takes 10 minutes in terms of the exact same math, your longest queue will be three minutes, five hours and 48 minutes versus three minutes just by adding one additional resource. So when I think of supply chain, I think of not just like what's bare minimum, but what's the acceptable amount of time that something has to take to get from a to Z and how many essentially bank tellers do you need to make sure that's within the acceptable amount of time. If it's like a call center, it might be under a minute, you know? So like, hey, how do you make sure you never get up to like a 15 minute queue or maybe your queue can be five minutes?
I think of like call centers or bank tellers, and I think of supply chain that kind of the same way of how, how early do I need to order my resources and how many bank tellers do I need for those resources to be able to process that. Right now I'm finding like the biggest problem is that quote unquote, we don't have enough bank tellers to even process the information. So the that's what's truly sending, and I wonder what the math is to just to get it within an acceptable range anyways, something I geek out on, but maybe we can have that on another time due to the time I'm looking at the clock here, this is a really fascinating topic. I'm expecting a lot of our audience to maybe get back with questions. We'll have you back on talking about supply chain on both from the Amazon perspective and to, just to get you back on a really fascinating topic, especially during the pandemic. I mean, jeez, so I'm grateful that you're able to come on and make that time for us. If you're going to give your final word advice to emergency managers, thinking about supply chain, business continuity, what is one thing that you'd really hope the field would understand?
Guest: Andrew Owlett (25m 32s):
You need visibility. You need visibility into who your suppliers are, what they do, how they map to critical functions that your organization has and there's really no better way to start then, you know, doing the BIA, like you said earlier, John, I mean, that's, that's such a fascinating place to begin do a rapid BIA, do something simple, and then at least get some, get some visibility, ask more questions, and then continue mapping out. What is your true supply chain risk and what does that look like? So my biggest word of advice.
Host: John Scardena (26m 6s):
Great. Call-out and I'm going to, I'm going to add one more that you, you said actually earlier, I want people to remind me, this is constant situational awareness, getting alerts, maybe adding some geospatial intelligence and understanding those systems, and you will really have great situational awareness so that you can move with disasters and prevent disasters from happening. Andrew, thank you so much for again, for coming on the show and talking with me for everybody's situational awareness became situational awareness. If you have a question for Andrew, you can always reach out to us on social media, Instagram, Facebook, Twitter, LinkedIn, obviously a LinkedIn's a really good one there because you can we'll tag Andrew. But if you have a question for him, you can put it there. You can also give us a five-star rating and if you liked this show would you should. If you have any questions that you don't want for the general population, because you're too afraid to ask or otherwise you shouldn't be because we're a good community, but you can always send us an email at info@dobermanemg.com and we'll send it over to Andrew and hopefully get your answer your question, and we'll see you next week.